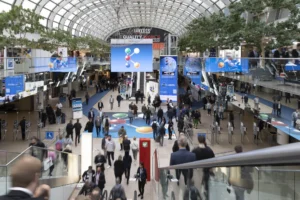
The MK6 represents the 6th generation of JETMASTER Series Servo Drive injection molding machines. Clamping mechanism, machine base, and injection unit have been significantly enhanced and strengthened to achieve superior efficiency and overall stability.
MK6-series machines employ SVP/3 servo-hydraulic technology that typically delivers 80% energy savings on average compared to older fixed displacement machines.
Precision HydraulicsTM realises repeatability within 0.05% in critical movement axes, helping clients increase their productivity and products’ acceptance rate.
Case study
TTI Group jumped from 90% to 98.8% acceptance rate, CH machines have proven themselves to be more competitive.
High efficient Servo motors reducing energy consumption up to 80%, bringing high precision and super low noise operation.
Larger space between tie bars (tie rods clearance), maximized storks bringing molders the ability of production with various molds.
Redesigned platen providing better distribution of clamping stress, lighter and faster operation and longer life.
Redesigned Ejector system providing the SPI standard and plenty of room to work with the ejector rods, which allows faster mold setup than ever.
Injection unit based on the bearing guides, providing better performance, absorbing of stress and even operation of the injection dual cylinders.
High pressure injection and fast speed recovery save seconds on cycle time.
Ergonomic well designed safety doors and covers maximizing the room for operation and maintenance.
Low maintenance requirement, repeatable and reliable production.
Machine Model | US Tons | Platen Size (in) | Tie Rod Clearance IN | Opening Stroke IN | Max daylight IN | Min-Max Mold Height IN | |
---|---|---|---|---|---|---|---|
Focus 60 | 66 | 17.72×17.72 | 12.2×12.2 | 10.63 | 23.62 | Download | |
JM88-MK6 | 97 | 21.26×21.26 | 14.17×14.17 | 13.38 | 28.34 | 4.92-14.96 | Download |
JM128-MK6 | 141 | 23.62×23.62 | 16.14×16.14 | 14.96 | 32.67 | 5.9-17.71 | Download |
JM168-MK6 | 185 | 26.77×26.77 | 18.5×18.5 | 17.71 | 38.18 | 6.69-20.47 | Download |
JM208-MK6 | 229.2 | 31.1×31.1 | 20.86×20.86 | 20.07 | 41.73 | 7.08-21.66 | Download |
JM258-MK6 | 284.4 | 33.07×33.07 | 22.83×22.83 | 22.04 | 44.88 | 7.48-22.84 | Download |
JM328-MK6 | 361.5 | 37.4×37.4 | 26.77×26.77 | 25.98 | 52.75 | 8.85-26.77 | Download |
JM398-MK6 | 438.7 | 39.37×39.37 | 28.74×28.74 | 28.34 | 57.08 | 9.84-28.74 | Download |
JM468-MK6 | 515.8 | 45.67×45.67 | 32.67×32.67 | 32.28 | 65.74 | 11.81-33.46 | Download |
JM568-MK6 | 626 | 47.63×47.63 | 33.85×33.85 | 34.25 | 66.11 | 13.78-33.85 | Download |
JM650-SVP/2 | 716 | 51.57×51.57 | 35.43×35.43 | 36.22 | 72.04 | 13.78‐35.82 | Download |
JM668-MK6 | 736.3 | 50.78×50.78 | 36.22×36.22 | 36.22 | 72.04 | 19.46-35.82 | Download |
JM800-C3-SVP/2 | 881 | 56.69×56.69 | 39.37×39.37 | 40.35 | 82.67 | 15.74-42.32 | Download |
JM1000-C3-SVP/2 | 1102 | 61.81×61.81 | 43.3×43.3 | 45.27 | 92.51 | 17.71-47.24 | Download |
JM1200-C3-SVP/2 | 1322 | 70.86×70.86 | 49.21×49.21 | 51.96 | 103.14 | 19.68-51.18 | Download |
JM1400-C3-SVP/2 | 1543 | 77.16×77.16 | 57.1×53.14 | 59.05 | 116.13 | 25.59-57.08 | Download |
JM1600-C3-SVP/2 | 1763 | 85.03×85.03 | 59.05×59.05 | 62.99 | 125.98 | 27.55-62.99 | Download |
Model ID | Screw L/D ratio L/D | Shot size (PS) Ounces | Screw Stroke Inches | Screw Rotation Speed RPM | |
---|---|---|---|---|---|
Focus 60 | 18~22 | 2.05~314 | 5.12 | 240 | Download |
JM88-MK6 | 18.3~24.4 | 4~7 | 7.08 (180) | 280 | Download |
JM128-MK6 | 18.7~23.9 | 6~11 | 8.07 | 250 | Download |
JM168-MK6 | 18.6~23.6 | 9~16 | 9.05 | 224 | Download |
JM208-MK6 | 18.2~23.7 | 13~24 | 10.23 | 200 | Download |
JM258-MK6 | 18.2~23.7 | 13~24 | 10.23 | 200 | Download |
JM328-MK6 | 18.8~23.5 | 30~47 | 13.19 | 200 | Download |
JM398-MK6 | 19~23.5 | 42~65 | 14.76 | 190 | Download |
JM468-MK6 | 19.4~23.2 | 58~72 | 16.33 | 180 | Download |
JM568-MK6 | 19.4~23.2 | 58~27 | 16.33 | 180 | Download |
JM650-SVP/2 | 20.2~23.9 | 74-104 | 16.73 | 152 | Download |
JM668-MK6 | 20.2~23.9 | 78~109 | 17.71 | 170 | Download |
JM800-SVP/2 | 19.6~24 | 94~142 | 18.11 | 110 | Download |
JM1000-SVP/2 | 20.2~24.7 | 127~191 | 20.47 | 113 | Download |
JM1200-SVP/2 | 20~24 | 184~259 | 20.47 | 113 | Download |
JM1400-SVP/2 | 20~24 | 246~325 | 25.59 | 89 | Download |
JM1600-SVP/2 | 20~24 | 301~402 | 27.55 | 85 | Download |
Choose your options:
Stay in touch and get the latest from CH America. Stay informed with product updates, launches, news, trade shows and much more.
CH America has several warehousing locations nationwide in addition to our 40,000 square foot corporate office and warehouse in Torrington, CT, 110 miles northeast of New York City and 100 miles southwest of Boston.
From the new DMZ multi-material series to the iChen™ Smart Family, we’re bringing together smarter, faster, and more connected solutions that transform production.
Service | Cookies | Description |
---|---|---|
Google Analytics | _gat_gtag, _ga, _gid | Used to distinguish users and sessions for web statistics purposes. |
Service | Cookies | Description | |
---|---|---|---|
Google Analytics | _gat_gtag, _ga, _gid | Used to distinguish users and sessions for web statistics purposes. |
Choose Your Region
The Chen Hsong Group has offices and distributors all around the globe.
Select your region from below or search our global list of distributors.